Leather
MIZ EXPORTS Pakistan proudly presents itself as a leading leather manufacturer and exporter company of premium quality leather garments & made ups. Designed as per the latest trends and fashion, our garments are a hit among all the fashion conscious men’s and women’s of today.
Process of making leather:
Leather manufacturing goes through the three sub-processes to cure the leather:
- Preparatory stage.
- Tanning process of leather.
- Crusting
A) Preparatory stages:
1. Curing:
Hides are first prepared by curing them with salt. To stop the raw hides and skins from deteriorating, they are preserved before the leather-making process begins. Apart from using salt, other methods of preservation include chilling, freezing, and the use of biocides.
2. Soaking:
The cured hides or skins are then soaked in clean water to remove the salt. Soaking can be from several hours to several days. This allows the hides to reabsorb any water they may have lost in the curing process or during transportation. It also helps to clean them of salt and dirt.
3. Liming:
It is the process where the leather is soaked in an alkali solution. It is done in a drum and it is to remove the hair and epidermis from the hides and also proteins and natural fats and grease. This process normally takes about eighteen hours for cattle hides.
4. Painting:
It is a method by which wool can be removed from sheepskins using a sulfide-based mixture.
5. Fleshing:
The step after liming is fleshing. The pelt is passed through a machine to remove fleshy tissue from the flesh side. If the hides are thick, they may be split into layers at this stage or after tanning.
6. Delimbing:
It is the next step. Acids are used and these could be weak acids like boric acid, acetic, formic, lactic acid, phosphoric acid, and carbonic acid. The principal purpose of delimbing is to gradually neutralize the alkali in the pelt, thereby avoiding rapid changes in the pH level which could lead to distortion or disruption of the tissues. delimbing takes place over a long period, it greatly improves the removal of any remaining lime, scud (miscellaneous debris), and residual components which were broken down during liming.
7. Bating:
Bating is based on the use of enzymes and completes this process so that the pelt is flat, relaxed, clean, and ready for pickling and tanning.
The tanning processes contain the pelt to have a low acid level, so through pickling, a weak acid and salt solution is used to bring the pelt to a low acid state. Stronger pickling solutions are used to preserve pelts so that they can be stored or transported in a stable form over periods of several months.
Degreasing involves solvents or water-based systems that are used to remove excess grease before tanning.
B) Tanning Process of Leather:
Tanning converts the protein of the rawhide or skin into a stable material and permanently alters the protein structure of the hide. This means that the leather will not putrefy (rot) and is suitable for a wide variety of purposes. Tanning materials form cross-links in the collagen structure and stabilize it against the effects of acids, alkalis, heat, water, and the action of micro-organisms.
The three main tannings are:
- Mineral tanning using chrome
- Vegetable
- Aldehyde
1. Mineral or chrome tanning:
It is the most common tanning process of leather. A heavy metal, chromium, is used in the form of basic chromium sulfate. Chromium is bio accumulative, meaning it can build up in an organism over time.
2. Vegetable tanning:
In this process, Various plant extracts produce brown-colored leathers which tend to be thick and firm. This type of tannage is used to produce stout sole leather, belting leather, and leathers for shoe linings, bags, and cases.
3. Aldehyde tanning:
Aldehyde and oil tannages produce very soft leathers. This system is used to produce leather that can be dry-cleaned and also washable fashion leathers and chamois leather. Aldehyde leathers meet the needs of the automotive industry.
Other chemicals that might be used in the tanning process of the leather, are one or more of the following: Sodium sulfide, Sodium hydroxide, Sodium hydrosulfite, Arsenic sulfide, Calcium hydrosulfide, Dimethylamine, and Sodium sulphydrate. Biocides like pentachlorophenol might also be added to prevent bacterial growth.
C) Crusting:
Crusting is done when the skin is thinned, re-tanned and lubricated, culminating in the final sub-processes of drying and softening. These are the main additional processes of making leather.
1. Splitting:
Thick leather is passed through a splitting machine, which slices thicker leather into two layers. The layer without a grain surface can be turned into suede or it can have an artificial grain surface applied.
2. Shaving:
A uniform thickness is achieved by shaving the leather on the non-grain side using a machine with helical (spiral-shaped) blades mounted on a rotating cylinder.
3. Neutralizing:
removes any residual chemicals and prepares the leather for further processing and finishing. Additional tanning material may be applied to give particular properties which are required in the finished leather.
4. Dyeing of leather:
It is the most common tanning process of leather. A heavy metal, chromium, is used in the form of basic chromium sulfate. Chromium is bio accumulative, meaning it can build up in an organism over time.
5. Fat liquoring:
It introduces oils to lubricate the fibers and keep the leather flexible and soft. without these oils, the leather will become hard and inflexible as it dries out.
6. Samming:
Samming is the process where the water content is reduced to about 55%. This is done by passing the hide through a number of machines.
7. Stretching:
Through setting out, the leather is stretched out and the grain side is smoothed. This process further reduces the water content to about 40%.
8. Drying:
Leather is normally dried to have only 10-20% water content. This is achieved in a number of ways and each method has a different effect on the finished leather. Staking and dry drumming: A staking machine massages the leather to separate the fibers. This makes the leather softer and more flexible. To finish off, the leather is softened by tumbling it inside a rotating drum.
9. Buffing and Brushing:
Through mechanical rubbing, the flesh surface is removed to produce a suede effect or to reduce the thickness. In some cases, the grain surface is buffed to produce a very fine nap, e.g., nubuck leathers. After buffing, the leather is brushed to remove excess dust.
10. Finishing:
The aims of finishing are to level the color, cover grain defects, control the gloss and provide a protective surface with good resistance to water, chemical attack, and abrasion.
11. Surface coating:
The area of each piece of leather is measured by the machine. Before the leather is dispatched to the customer, final grading will be done. This grading will control the color intensity and uniformity, the feel of the leather, softness, visual appearance, thickness, design effects, and natural defects such as scratches.
Leather made-ups:
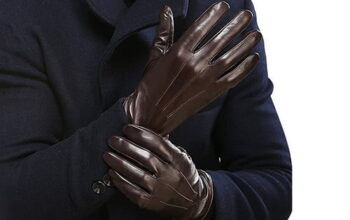
Leather Gloves
MIZ EXPORTS supplies leather gloves at a reasonable price that provides protection from occupational hazards. These gloves are useful in wet conditions, quick-drying, and leather remains soft.
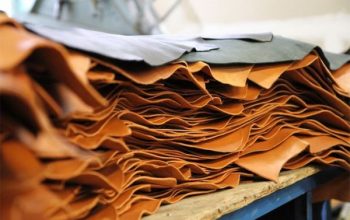
Raw Leather
We have developed ourselves because of the most promising manufacturer and exporter of Raw Leather. We can supply Cow, Buffalo, Goat, Sheep leather. We sell leather in black, beige, and yellow colors.
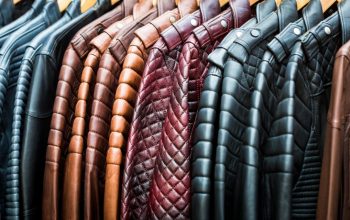
Leather jackets
MIZ EXPORT Men’s Leather Jacket collection has their popularity among subcultures like punk, pop, rock, and heavy metal; it’s where you’ll find a lot of customized genuine leather jacket men with studs and patches all over.
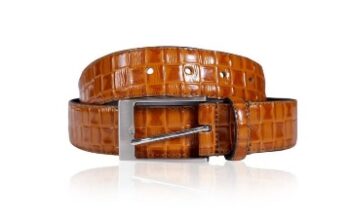
Leather Belts
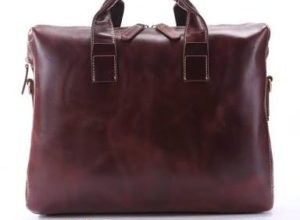
Leather bags
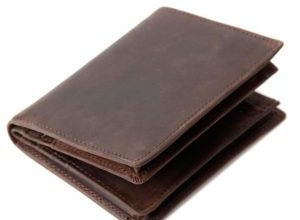
Leather wallets
Making Quality Leather Goods
We work hard to produce goods with beautiful Stitching and continually refine our processes. Selection of Leather and Stitching quality tells the quality of leather finished product. We have invested much time and money over the years both on tools and Our ability to use them, but we continue to refine and improve our techniques. We are proud of the products we make, but we also work towards continuously improving.
Frequently Asked Questions
Still open questions?
To order fill out our contact form, enter your name, email and message and then click submit.
Fill our quotation form, enter item name, container size, delivery city, country, phone number, delivery time, quantity, email and the write the message then click on submit.
Please call or fill out the form to contact us, then our representative will contact you. Then we will share meeting schedule with you by email.
To plane a visit call us or fill out the contact form, then one of our representatives will contact you and share the visit schedule.
You benefit from our experience in delivering effective solutions to the complex global supply chains of some of the world’s biggest corporations.
You benefit from every innovation, whether it involves a simple extension to our Air and Ocean Freight products, whether it means a development in warehousing.
All of which explains why you’ll find the team of outstanding support at MIZ Exports ready to apply their passion for solutions in support of your business.